ERP or enterprise resource planning software are applications developed for manufacturing purposes. Manufacturing companies use it to manage manufacturing processes from the procurement of materials up to the shipment of goods. Manufacturing ERP ensures that manufacturing companies can transform raw materials into finished goods at a minimal cost while maintaining quality control.
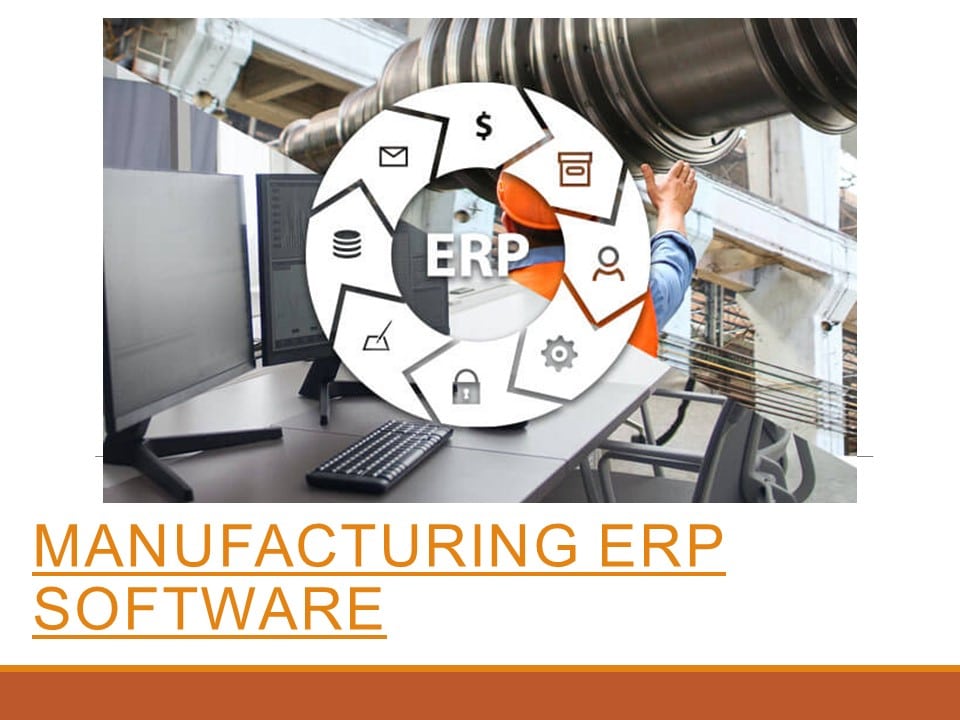
The manufacturing ERP software industry began in the 1960s when manufacturers began recording workflow processes on mainframe computers. With the ever-increasing demand for computerization, manufacturing ERP systems have become an integral part of business operations in any manufacturing organization. Key functionalities included in manufacturing ERP systems are sales and distribution, warehouse and inventory management, production planning and controlling, factory maintenance and manufacturing, and sourcing and procurement.
What are the differences between MRP, MRPII and ERP?
MRP (Material Requirements Planning), MRPII (Manufacturing Resource Planning), and ERP (Enterprise Resource Planning) are different stages and concepts within the evolution of systems used to manage and plan manufacturing processes. Here are the key differences between them:
Material Requirements Planning (MRP):
- Focus: Primarily focused on managing and planning material requirements for production.
- Functionality: Deals with inventory control, ensuring materials are available for production, and uses algorithms to calculate material requirements based on production schedules.
- Scope: Primarily addresses the material aspect of production planning and scheduling.
Manufacturing Resource Planning (MRPII):
- Enhancement of MRP: MRPII expanded the scope beyond material requirements to include other resources like manpower, machine capacity, and financial resources.
- Functionality: Includes modules for capacity planning, scheduling, workforce management, financial planning, and more, integrating various operational functions.
- Integration: Allows for the integration of material planning with other resources required for production.
Enterprise Resource Planning (ERP):
- Further Expansion: ERP further expanded on the capabilities of MRPII by integrating all aspects of an organization’s operations beyond manufacturing, including finance, human resources, supply chain, sales, and more.
- Holistic Approach: Aims to provide a comprehensive view of all business processes by integrating different functions into a single unified system.
- Cross-Functional Integration: Offers seamless integration of various departments and functions within an organization, facilitating data sharing and collaboration across the enterprise.
Key Differences:
- Scope: MRP focuses on material planning, MRPII expands to include resources beyond materials, and ERP encompasses all aspects of an organization’s operations.
- Integration: MRP deals mainly with materials, MRPII integrates material planning with other resources, and ERP integrates multiple functions across the entire enterprise.
- Functionalities: While MRP is primarily about inventory and material planning, MRPII includes capacity planning and financial aspects, and ERP extends to cover finance, HR, supply chain, sales, etc.
In essence, MRP laid the foundation for planning material requirements, MRPII expanded to incorporate broader manufacturing resources, and ERP took this a step further by integrating all facets of an enterprise’s operations into a unified system, offering a holistic view for efficient management and decision-making.
What are the benefits of using manufacturing ERP software?
Implementing manufacturing ERP (Enterprise Resource Planning) software offers several benefits to businesses in the manufacturing industry, enhancing operational efficiency, improving decision-making, and enabling growth. Here are the key benefits:
1. Streamlined Operations:
Integrated Processes: ERP software integrates various functions like production planning, inventory management, supply chain, and quality control into a unified system, streamlining operations.
2. Enhanced Visibility and Control:
Real-time Data: Provides real-time visibility into production processes, inventory levels, and resource utilization, enabling better control and decision-making.
Cross-departmental Insights: Enables managers to access comprehensive data across departments, fostering collaboration and informed decision-making.
3.Improved Efficiency:
Automation of Tasks: Automates manual tasks, reducing human errors and saving time.
Optimized Resource Utilization: Helps in better allocation of resources like materials, equipment, and manpower, optimizing efficiency.
4. Better Inventory Management:
Optimal Stock Levels: Helps in maintaining optimal inventory levels, reducing shortages or excess stock, and minimizing carrying costs.
Accurate Demand Forecasting: Allows for accurate forecasting of material requirements based on production schedules, reducing inventory holding costs.
5. Cost Savings:
Reduced Wastage: Minimizes wastage of resources and raw materials through efficient planning and inventory control.
Operational Cost Reduction: Enhances operational efficiency, leading to cost savings in production and supply chain processes.
6. Improved Quality Control:
Consistency and Compliance: Facilitates adherence to quality standards and regulatory compliance by implementing robust quality control measures at various production stages.
7. Enhanced Decision-Making:
Data-Driven Insights: Provides data analytics and reporting tools, offering actionable insights for better strategic planning and decision-making.
Quick Response: Enables faster response to market demands and changes in production requirements.
8. Scalability and Adaptability:
Flexibility: Offers scalability to adapt to changing business needs and growth, accommodating expansion without disrupting operations.
9. Customer Satisfaction:
Timely Deliveries: Helps in meeting delivery schedules by improving production efficiency, leading to enhanced customer satisfaction.
Conclusion:
Manufacturing ERP software serves as a comprehensive solution that addresses the complexities of manufacturing operations. By optimizing processes, enhancing visibility, and facilitating informed decision-making, ERP systems enable manufacturing businesses to improve efficiency, reduce costs, maintain quality, and stay competitive in an ever-evolving market landscape.